How To Estimate a Paint Job in 7 Easy Steps
Knowing how to estimate masonry work is essential for any construction professional or contractor. Whether planning to build a brick wall, undertake a restoration project, or execute a comprehensive masonry job, understanding how to estimate the costs involved is fundamental to project success. Assessing masonry work involves considering factors such as labor cost, material expenses, and the intricacies of estimating brick wall masonry.
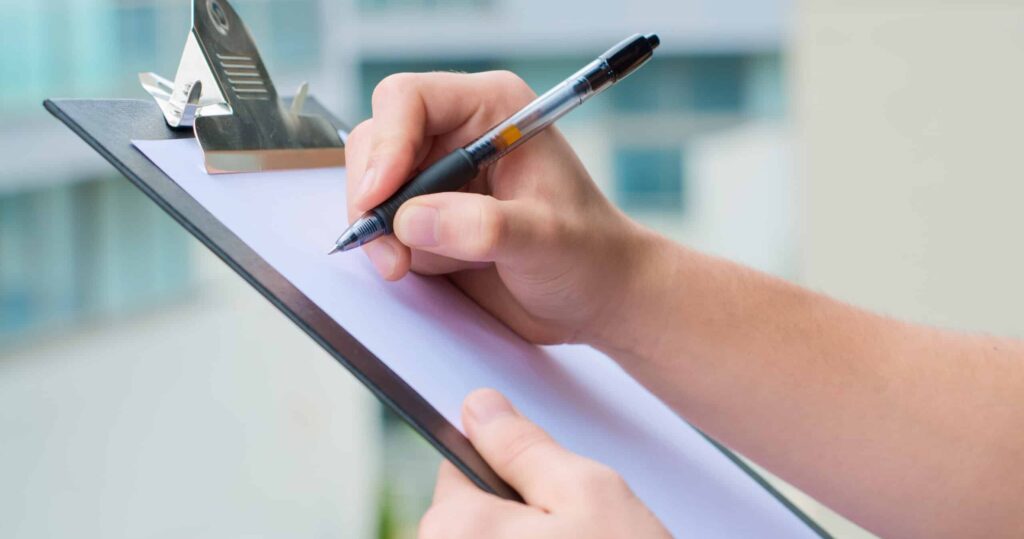
Step 1: Do Your Masonry Job Pre-Check
Before diving into a brick-wall masonry project, conducting prechecks is crucial to ensuring a smooth and successful process. These prechecks involve assessing various aspects of the project to gather valuable information.
Ask the Right Questions
By asking the right questions, such as the desired outcome, timeline, and budget, you can gain valuable insights into the client’s expectations and tailor your approach accordingly. Understanding their needs allows you to provide accurate masonry estimating and deliver satisfactory results.
Inspect the Current Site
It’s crucial to consider uncommon elements that may impact masonry estimating and overall project cost. Site conditions like soil composition, accessibility constraints, or the presence of existing structures can significantly affect the bottom line. By carefully evaluating these factors, you can make more informed decisions and ensure the estimate accurately reflects the project’s requirements.
Address Building Codes
Building codes are regulations that govern construction practices and ensure safety, durability, and compliance with legal requirements. Understanding the specific building codes relevant to masonry work is essential, including material specifications, mortar ratios, reinforcement guidelines, and structural requirements. By adhering to these codes, builders guarantee a structurally sound outcome and mitigate potential legal issues.
Step 2: Measure the Space
Precise space measurement is crucial in learning how to estimate masonry work. Here are key considerations and often neglected factors to keep in mind:
- Length, Width, and Height: Ensure precise measurements to avoid underestimating or overestimating material quantities, like using the correct amount of concrete masonry units for a proposed wall.
- Thickness: Remember to measure the thickness of straight walls, foundations, or other masonry elements, as it’s essential for calculating the materials needed. These units may require additional considerations for wall reinforcement.
- Doors and Windows: Consider the openings within the masonry area. Measure their dimensions to plan for necessary adjustments or accurate framing.
- Slopes and Angles: If the brick masonry work involves sloping wall surfaces or angled structures, measure and account for these variations, like inclined walls or chimneys.
- Niche and Recessed Areas: It’s important to measure these spaces, as they require additional materials and specialized installation techniques, affecting the needed square footage.
- Expansion Joints: Measure and plan for the appropriate placement and size of expansion joints, especially for large structures or areas prone to movement.
- Archways and Curves: Measure the radius or dimensions of these features accurately. Pay special attention when calculating the necessary materials and executing precise construction.
- Net Wall Areas: Calculate the net wall areas by deducting the space occupied by doors, windows, archways, and curves from the total wall surface area. You’ll get a more accurate estimation of the masonry materials needed for the wall sections.
- Miscellaneous Factors: Pay attention to irregular wall shapes, rounded corners, or non-standard masonry elements. These may require additional measurements and considerations for accurate estimates involving the total square footage of the specific parts.
By considering all these factors and measuring the space thoroughly, you can ensure a more precise estimation of concrete masonry units needed or other materials and labor, reducing the likelihood of costly surprises or delays during the masonry project.
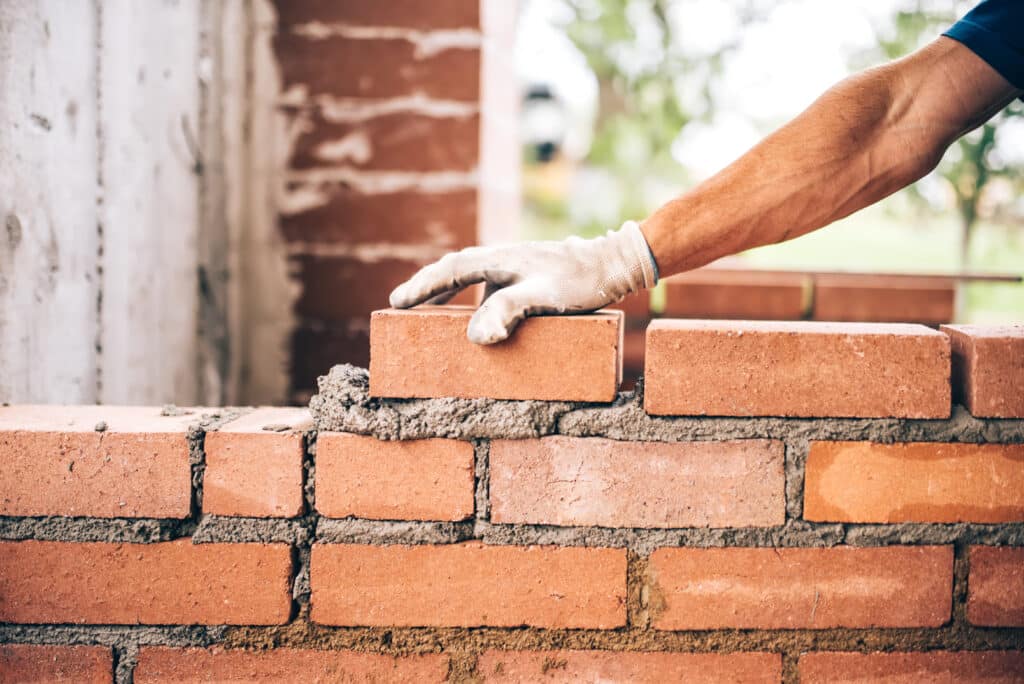
Step 3: Estimate Masonry Material Costs
Estimating material costs is a crucial aspect of planning a masonry project. It includes accurately understanding the required materials like bricks and natural stone, plus associated expenses.
Tips for Estimating Brick Material Costs
One aspect to consider is the form of the bricks and concrete masonry units. Unusual shapes or patterns may require additional cutting or specialized installation techniques, impacting the overall cost. Extra equipment and scaffolding may be necessary when dealing with elevated areas, like high structures, leading to added labor and rental costs. It would be best to account for extra bricks or concrete masonry units to reduce the risk of under-purchasing.
This buffer is vital for matching colors, accommodating damaged bricks, or accommodating changes that may arise during the construction process per square foot. By incorporating these potential issues and accounting for additional masonry units, you can improve your cost estimation accuracy and ensure a smoother project execution.
Interior vs. Exterior Masonry Costs
Exterior Masonry Work | Interior Masonry Work |
Typically requires specialized materials and techniques for weather resistance, durability, and aesthetic appeal, leading to higher material costs. | Less exposed to environmental factors, reducing the need for certain specialized materials and protective measures. |
Involves additional preparation and protection against external elements, increasing labor and overall project expenses. | Considerations like structural support or design requirements specific to the space may influence the overall cost. |
Tips for Cleaning/Preparation Costs
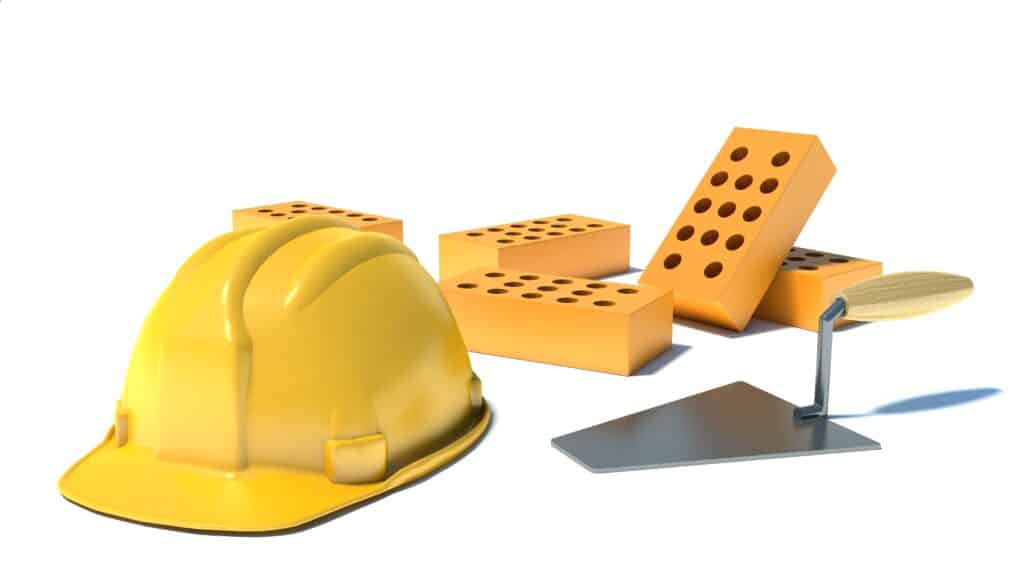
Estimating the costs for cleaning and preparation in a masonry job is essential to ensure a well-prepared surface for construction or restoration. It includes removing dirt, debris, or old coatings from the wall surface. Depending on the condition of the existing structure, pressure washing or other cleaning methods may be necessary, which can incur additional expenses.
The cost estimation should also account for surface repairs, such as patching or leveling uneven areas. Considering the type and quality of cleaning agents, sealants, or primers required for the specific project is important in accurately estimating the cleaning and preparation costs.
Tips for Estimating Supporting Material Costs
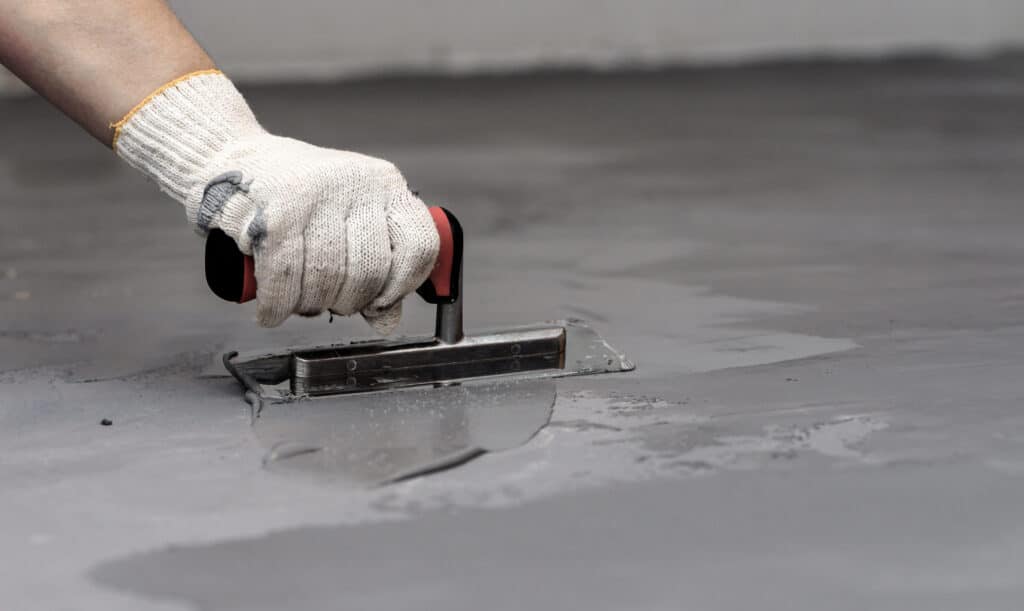
Estimating extra material costs beyond bricks and preparation items is crucial to ensure a smooth and well-executed masonry project.
How to Calculate Mortar in Brick Masonry
Follow these steps to calculate the amount of mortar needed for brick masonry:
- Determine the brickwork’s volume by multiplying the brick wall’s length, width, and height.
- Select the mortar-to-brickwork ratio, typically 1:3, which means one part cementitious material to three parts sand. Multiply the volume of the brickwork by the mortar ratio to obtain the total volume of mortar required.
- Consider factors such as joint thickness, mortar waste, and adjustments during construction to ensure accurate calculations and reduce the likelihood of under-purchasing mortar.
How to Calculate Sand for Brick Masonry
Calculating the quantity of sand required for brick masonry is a straightforward process:
- Calculate the volume by multiplying the brick wall’s length, width, and height.
- Choose the sand-to-cementitious material ratio, typically in the range of 2:1 to 4:1.
- Multiply the volume of the brickwork by the sand ratio to obtain the total volume of sand needed.
Consider factors such as the type of sand and any adjustments required based on specific project conditions to ensure accurate calculations for a successful brick masonry endeavour.
Extra Material Costs
Additional supplies may include wall reinforcement materials, grout, insulation, or specialized additives. Accurate estimation requires accounting for the quantity and cost of these extra materials, ensuring that the project is adequately supplied and avoiding potential delays or shortages during construction.
Estimating Software for Masonry: Try for Free
Step 4: Estimate Labor & Rental Costs
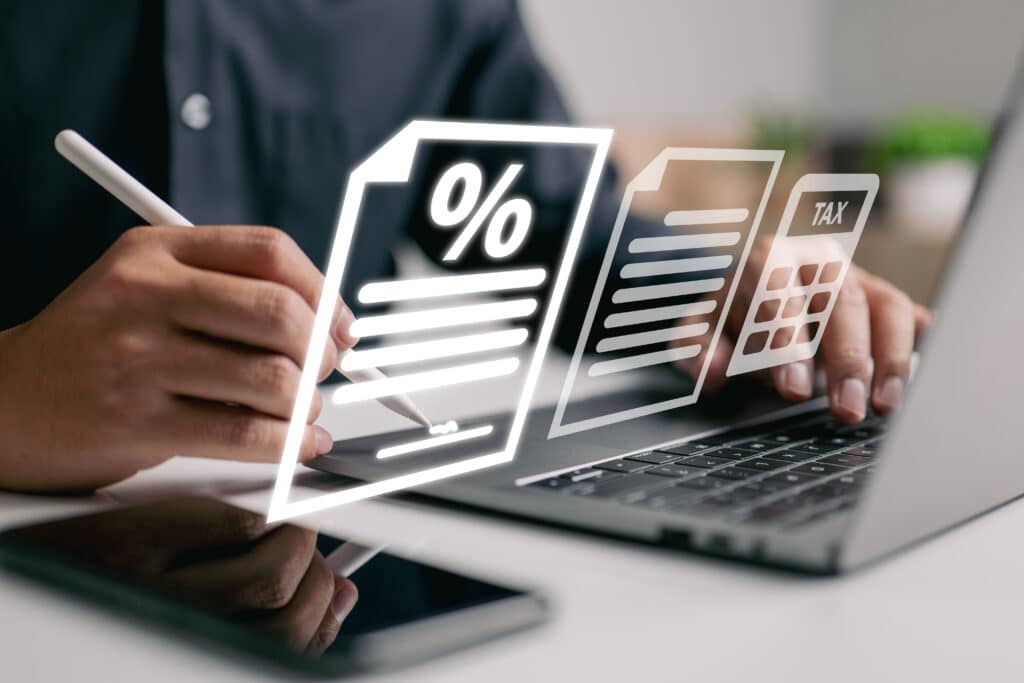
Labor and rental costs, often considered the “cost of doing business,” are significant in determining the project’s budget.
Estimating Labor Costs
When estimating labor costs for masonry projects, it is crucial to consider numerous factors influencing the overall expenses. These factors may include the extra time required for thorough cleaning and preparation, working in hard-to-access areas, last-minute add-ons, or demolishing existing structures. By accounting for these considerations, you ensure a more accurate estimation of labor costs and prevent any unexpected budgetary surprises.
Estimating Rental Costs
Renting specialized equipment or tools can be cost-effective for masonry projects. To estimate rental costs effectively:
- Remember the tools needed, their rates, and the rental period.
- Factor in additional charges like delivery or maintenance fees.
- Consider important factors availability or renting from multiple sources for competitive pricing.
Careful estimation of rental costs helps optimize your budget, ensures access to necessary equipment, and contributes to a smooth and efficient masonry project execution.
Step 5: Account for Overhead & Profit Margin
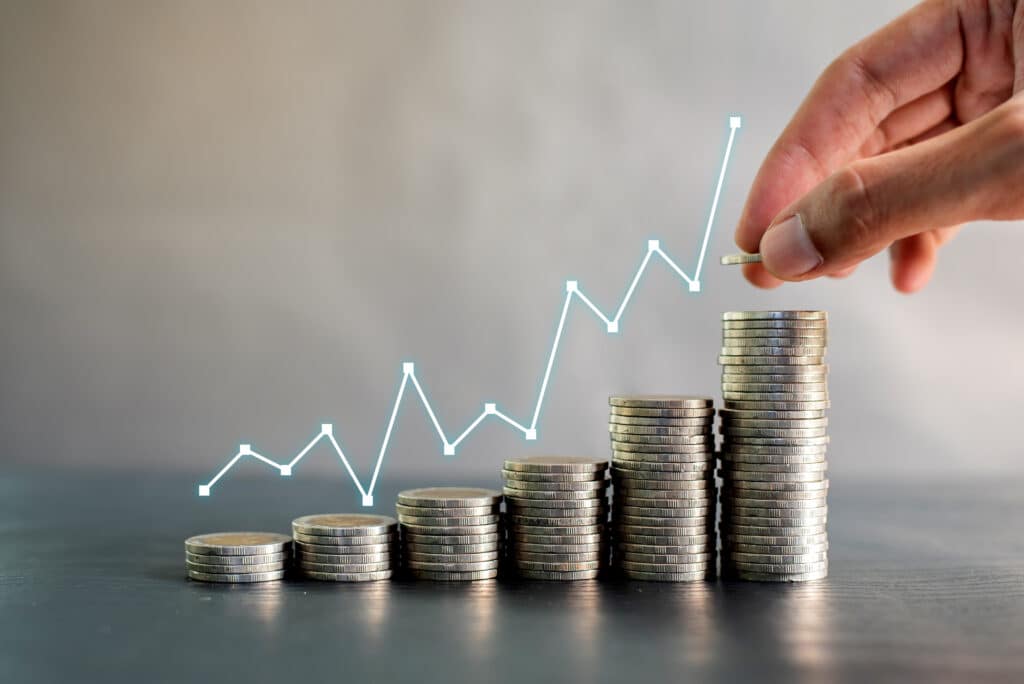
This process involves determining the business’s costs and setting profit goals. By accurately calculating overhead and establishing an appropriate profit margin, masonry contractors can ensure competitive pricing, cover operating expenses, and achieve financial objectives.
Determining Overhead
Calculate your hourly overhead costs by dividing your yearly overhead costs by the number of billable hours per year. We use a full year to calculate overhead to address businesses affected by the seasons.
Total Yearly Overhead Costs ÷ # of Billable Hours per Year (Total Number of Employees x Hours They Work Over the Week x 52 Weeks) = Hourly Overhead Costs
For example, suppose your mason business’s yearly overhead costs are $42,000, and we divide it by your team’s 4,800 billable hours a month. In that case, your hourly overhead costs are $8.75. Once you’ve determined your hourly overhead cost, you’ll use that to decide on your overhead costs per job. To calculate the overhead costs for an individual masonry job, use the formula below:
Hourly Overhead Costs x # the Hours to Complete the Job = Overhead Cost for the Job
If a masonry job takes three and a half hours to complete, we will multiply $8.75 by 3.5 for a total overhead cost of $30.63 (rounded up).
By considering the below items, brick masons can accurately assess the actual costs of their business operations and set competitive pricing that covers all necessary expenses while maintaining a healthy profit margin:
- Business equipment such as computers, printers, or cell phones
- Rent and utilities for office or workspace
- Salaries for administrative staff, project managers, and other employees
- Permits and licenses required for operating the masonry business
- Vehicles, fuel, and maintenance for transportation of materials and equipment
- Taxes and business insurance to comply with legal obligations and protect the business
- Advertising and marketing expenses to promote the masonry services
- Business management software for efficient project tracking and administration
- Credit card processing fees for accepting payments from clients
- Employee benefits, including health insurance and retirement plans
- Masonry tools and equipment (e.g., trowels, levels, saws, scaffolding) necessary for various projects
- Employee Training and Certifications
- Costs associated with training employees to stay updated on masonry techniques and safety standards.
- Safety Equipment and Gear
- Expenses for purchasing and maintaining safety equipment, such as helmets, gloves, and protective clothing, to ensure a safe working environment.
- Material Storage and Handling
These are the costs related to renting or maintaining storage facilities for masonry materials and handling equipment like forklifts or cranes.
Calculating Masonry Profit Margin
To calculate your existing profit margin, start by calculating your net profits by using this formula:
Total Revenue – Material Costs – Labor Costs – Overhead Costs = Net Income
Once you have your net income, you can simply determine your profit margin using this formula:
Net Income / Total Revenue = Profit Margin
To include your profit margin on the cost of materials for a particular job, use the formula below:
Total Project Material Costs* + (Total Project Material Costs* x Profit Margin) = Total Project Pricing *Total project material costs include labor.
You can begin to set ambitious, achievable goals based on your current profit margin per square foot. It would help if you determined which profit margin will help your masonry business reach its financial goals.
What Is the Ideal Profit Margin for a Masonry Job?
The ideal profit margin for a masonry job varies depending on your business’s financial needs. While average profit percentages may be available, the “ideal” margin will be specific to each contractor’s goals and requirements. To find a suitable profit margin that aligns with your business objectives, refer to industry resources for estimated percentages while considering your unique financial situation.
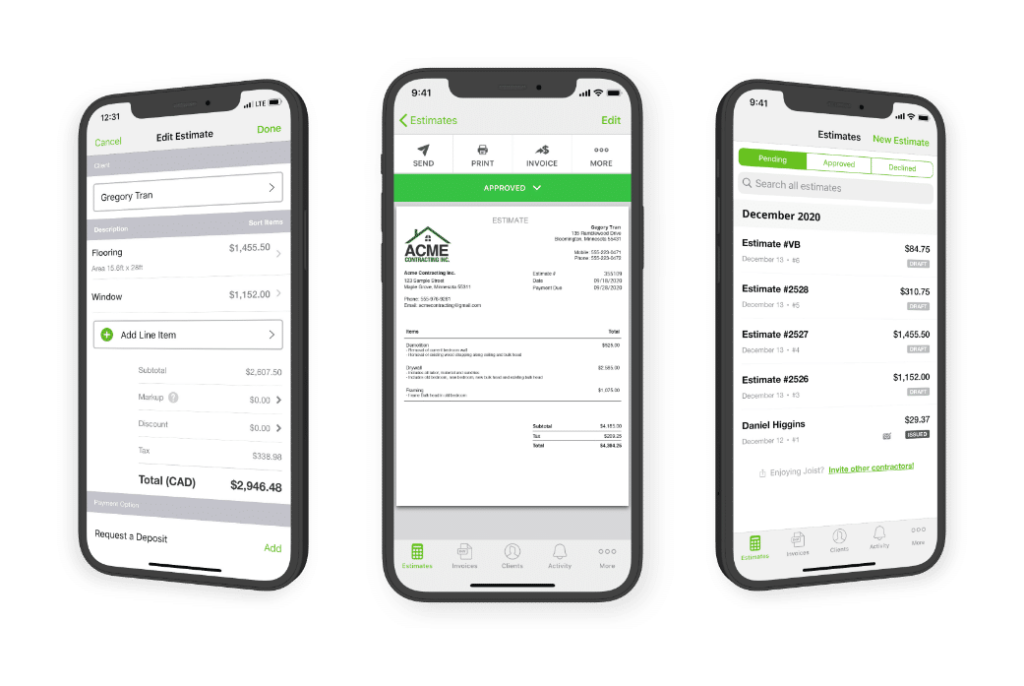
Step 6: Create the Masonry Estimate
Creating a formal estimate is a crucial step in the masonry process, ensuring clear communication with clients and providing a comprehensive breakdown of project costs.
How to Write an Estimate for a Masonry Job
When writing the estimate, include higher-level cost items to provide a detailed overview of expenses. Some essential items to include are:
- Labor costs, accounting for different skill levels and project phases
- Material costs, specifying the type and quantity of bricks, mortar, sand, and additional materials in cubic feet
- Rental prices for any specialized equipment or tools required
- Overhead expenses, such as business operation costs and administrative fees
- Profit margin, calculated based on individual financial goals and business needs
Masonry Work Estimate Template
Using a well-designed estimate template enhances professionalism when presenting proposals to clients. The template should include:
- Business logo and contact information for brand recognition
- A detailed breakdown of labor, material, rental, and overhead costs
- A clear description of the project scope and specifications
- Terms and conditions, outlining payment terms and project timeline
By following these steps and utilizing a professional template, contractors can create accurate and visually appealing masonry estimates that build client trust and streamline project planning.
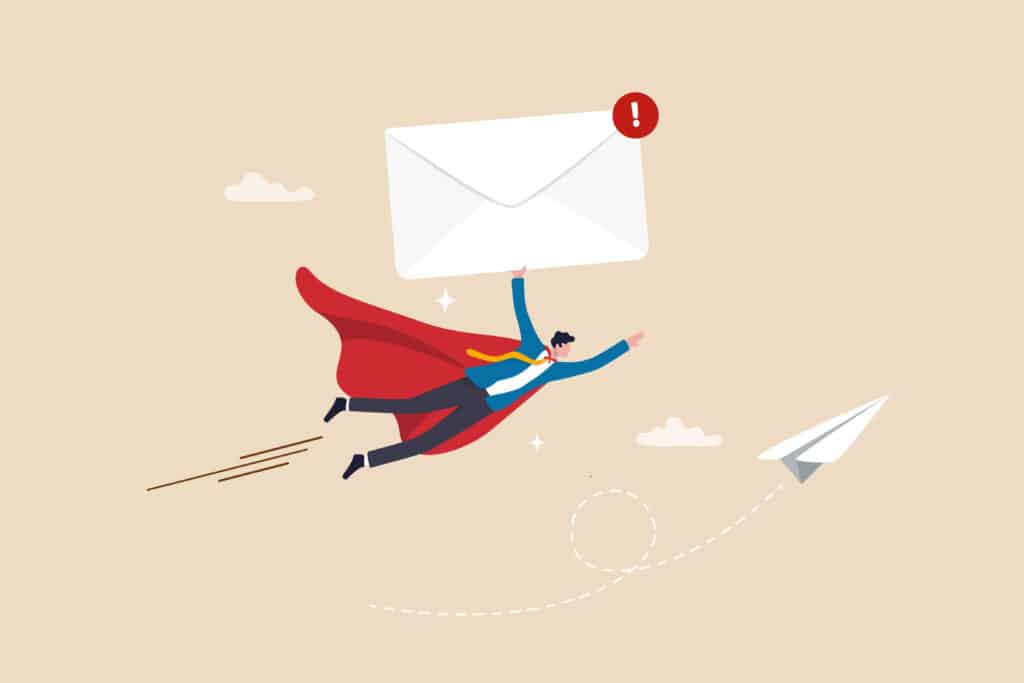
Step 7: Deliver the Estimate
Delivering the estimate to potential customers is critical in securing masonry projects. To ensure a positive reception, consider the following tips:
- Clear Communication: Clearly explain the estimate’s breakdown, detailing the scope of work, material costs, labor, and other expenses. Avoid technical jargon and use simple language for easy understanding.
- Visuals and Documentation: Incorporate visual aids, such as project sketches or images, to help clients visualize the proposed work. To build trust and credibility, provide any necessary documentation, such as licenses, insurance, and references.
- Prompt Response: Deliver the estimate promptly after the initial inquiry to show professionalism and commitment to the project.
- Personalization: Tailor the estimate to the client’s specific needs and preferences. Address any concerns and offer flexible options to accommodate their budget.
Two Sales Tips for Brick Masons:
- Showcase Expertise: Demonstrate your masonry expertise and display past successful projects to instill confidence in your skills and capabilities.
- Highlight Value: Emphasize the long-term benefits of quality craftsmanship, durability, and aesthetic appeal that your masonry services offer, positioning them as a valuable investment for clients.
By delivering estimates in a customer-focused manner and utilizing effective sales strategies, you can establish a strong rapport with potential clients, increasing the likelihood of winning contracts and building lasting business relationships.
Need to create a professional masonry estimate?
Joist can help.